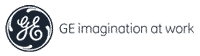
16 Nov 2005
GE - Plastics and GE – Advanced Materials, Silicones Expand Commitment to Healthcare Customers with Investments in Facilities, Services and Products
Skin Stapler, Enteral Feeding System, and Plastic Resin and Silicone Grades on Display in GE Booth at Medica Düsseldorf
BERGEN OP ZOOM, THE NETHERLANDS ― November 16, 2005 ― GE - Plastics and GE – Advanced Materials, Silicones will discuss recent investments in technology and expertise and showcase their latest innovations for medical device manufacturers at Medica in Düsseldorf, Germany from Nov. 16-19. In hall 10, booth A56, the two GE businesses will feature some of their customers’ innovative products utilizing GE’s resins and silicones. This will include items such as the INSORB®|20 subcuticular surgical stapler and Zevex International’s enteral feeding system. Two new grades of Lexan* polycarbonate (PC) resin will also be featured.
“GE’s Plastics and Advanced Materials, Silicones businesses have continued building capabilities to help our customers turn their innovative designs into application successes,” said Clare Frissora, market director, Healthcare for GE - Plastics. She adds, “GE – Plastics and GE – Advanced Materials, Silicones have committed support to the industry by investing in new technical capabilities, materials technologies and dedicated healthcare teams for healthcare specific support for our customers worldwide. New materials and technical capabilities are designed to respond to the evolving trends and needs of the healthcare industry. We look to GE - Plastic’s 20 percent product portfolio for the healthcare industry as an example of this focus.”
In the past year, GE’s new biocompatible(1) products have been developed to help offer better resistance to lipids, enhanced flow and release properties, improved sterilization capabilities, and excellent overall materials performance. GE – Advanced Materials, Silicones has added additional silicone capacity in Germany and Thailand to help support global healthcare customers. The company also expanded its Garrett, Ind. and Shanghai, China facilities to offer customization of high-consistency and liquid silicone elastomers, including formulating, mixing, compounding, and blending capabilities to customers serving the healthcare industry.
“We’ve also tripled the size of our global teams dedicated to the healthcare industry to support our customers in their endeavors,” said Eric Luftig, Healthcare marketing manager, GE – Advanced Materials, Silicones. “Today, we have a greater number of dedicated resources, a deeper and broader talent pool, and are in an outstanding position to help anticipate industry trends and meet customer challenges.”
GE’s Materials Help Provide a Competitive Advantage
With its broad and deep global R&D, design and manufacturing capabilities, GE’s Plastics and Advanced Materials, Silicones businesses excel in helping healthcare device designers and OEMs gain a competitive edge by providing materials solutions that differentiate their products. GE facilitates speed to market and efficient application development by helping customers as they work through the many stages of product design, application development, and manufacturing set-up. For example, GE supported Incisive Surgical, Inc. over an 18-month period as Incisive Surgical completed development on its INSORB|20 subcuticular skin stapler – a new offering that demonstrates the capabilities of plastics vs. the traditional use of metal.
Other success stories include Zevex International's enteral feeding system. GE worked with Zevex on their latest disposable dosing tube that is a key component of the company's award-winning EnteraLite Infinity enteral feeding system. Injection-molding the part from GE’s LIM 6050-D2 material instead of extruding it made possible Zevex’s complex, patent-pending design, that provides precise volumetric accuracy, allows the use of alarm sensors for detecting occlusions or free flow, and makes replacement a "snap" for consumers. The new device recently won a Medical Design Excellence Award at the MD&M East show in New York City.
Technologies Anticipate Healthcare Trends
Included in the trends impacting the healthcare industry are an aging population; short hospital stays driving towards the need for advanced in-home-care; disposable devices requiring a high level of material performance; the ongoing challenge to balance total system cost challenges; and the increasing importance of aesthetics, light weight, and ergonomics. These trends are demanding new designs and technology must evolve to support them. Rather than react to these trends, GE maintains dedicated healthcare teams to track global advances and anticipate responses needed to serve emerging application and regulatory needs.
GE - Plastics is demonstrating the capabilities of resins vs. the traditional use of metals, enabling the trend toward lighter weight material options, yet allowing high precision and performance. Applications featured are the INSORB|20 subcuticular skin stapler, utilizing Ultem* resin, and other applications such as surgical instrument components including gears, levers and handles, sterilization trays and wrist fixation devices, all belonging to segments with historical use of metal. To help deliver excellent clarity, impact strength, and durability, Bioject® selected GE’s Lexan resin, and, for its Biojector® 2000 needle-free drug delivery injection devices, they chose Cycoloy* resin for its balance of impact resistance and other mechanical properties.
Aging consumers are just one group that may benefit from breathable shoe insoles from Implus Footcare. The Airplus® Invisigel™ insoles are molded from GE’s LSR liquid silicone rubber to provide a soft feel and conformity to the foot for exceptional comfort. GE’s LSR Topcoat allows the foot to slip easily into a shoe lined with the Invisigel insole, and reduces the build-up of dust. LSR Top Coat continues to find new applications in orthopaedics in combination with new RTV products. For example, new low hardness RTV rubbers provide high strength for orthopaedic liners and can be top coated to obtain a skin-like surface for improved ergonomics and comfort. The new range of RTV Gels are used in multiple pressure care applications where Topcoat is used to reduce tackiness of the geal surface. Examples will be displayed here at Medica Düsseldorf.
New Materials Available for Manufacturers
Another key trend involves the healthcare industry’s demand for higher-performing materials to meet the growing use of autoclave sterilization. GE’s new biocompatible Lexan resin grades, Lexan HPX4 and Lexan HPX8R PC resins help meet this demand along with improved flow and release capabilities. These grades join GE’s range of materials for use with autoclave sterilization, including other selections from Lexan PC resins, as well as Ultem polyetherimide resins, Noryl* PPO* blend resins, and LNP*’s Colorcomp*, Thermocomp*, and Lubricomp* compounds. The need for improved flow is met with the new Lexan HP1HF resin grade with a 35 MFI (melt flow index).
When manufacturers face the tough challenges posed by exposure to blood and fluids, GE offers a broad range of materials that can help them overcome these challenges. The chemical resistance to blood provided by Ultem 1000 resin, along with its high tensile strength, met the requirements of WaisMed’s Medical Bone Injection Gun.
For companies looking to balance productivity with enhanced mechanical performance and compliance, GE – Advanced Materials, Silicones offers a new family of platinum curable, high clarity, extrusion grades in the new Addisil* elastomers series. The new Addisil elastomers portfolio provides a full range of extrusion products that consists of one component or two-component systems, with a hardness range from 50-80 Shore A, to cover the needs of multiple applications. This new technology helps deliver peroxide-free, fast-curing systems with a great balance of properties for use in a variety of tubing applications in the healthcare and pharmaceutical space.
For peristaltic pumps found in fluid delivery devices and pharmaceutical processing systems, GE’s new Tufel* III silicone offers a platinum curable silicone elastomer with enhanced physical properties: low compression set, low hysteresis, and high bayshore resilience. This may translate into longer and more consistent pump life performance vs. traditional platinum elastomers.
GE Toshiba Silicones has launched a new liquid silicone portfolio, Tiger LSR 48XX liquid silicone rubber series available in 40 through 70 durometers. This portfolio offers high tear strength, fast cure, and low viscosity which could be used in, but not limited to, injection-molded healthcare applications such as urological catheters, filters, diaphragms, wound drain bulbs, sterilization mats, and respiratory masks.
The growing global importance of medical electronics is another key growth area for GE’s Advanced Materials, Silicones business. The company is already leading the charge here with a new portfolio of high-performance silicone products for a broad range of electronics applications to help designers assemble, protect, and enhance their devices.
Finally, GE’s LSR Top Coat two component liquid silicone coating provides lower coefficient of friction when used in conjunction with silicone elastomer substrates. LSR Top Coat coating can be applied by spray, brush, or dip coating techniques and is featured in the Airplus Invisigel orthopaedic insoles. This coating can also help reduce friction in other healthcare products such as respiratory devices, orthopeadic applications, and fluid delivery systems.
Reader enquiries
GE PlasticsPlasticslaan 1
4600 AC Bergen op Zoom
Netherlands
Helen Vandebovenkamp
helen.vandebovenkamp@ge.com
Tel: +31 164 29 20 97
Fax: +31 164 29 10 66
Netherlands
+31 164 29 20 97
helen.vandebovenkamp@ge.com
www.geplastics.com
Notes for editors
About GE - Plastics
GE - Plastics is a global supplier of plastic resins widely used in automotive, healthcare, consumer electronics, transportation, performance packaging, building & construction, telecommunications, and optical media applications. The company manufactures and compounds polycarbonate, ABS, SAN, ASA, PPE, PC/ABS, PBT and PEI resins, as well as the LNP line of high-performance specialty compounds. GE - Plastics, Specialty Film & Sheet manufactures high-performance Lexan sheet and film products used in thousands of demanding applications worldwide. In addition, GE - Plastics’ dedicated Automotive organization is an experienced, world-wide competitor, offering leading plastics solutions for five key automotive segments: body panels and glazing; under the hood applications; component; structures and interiors; and lighting. As a Worldwide Partner of the Olympic Games, GE is the exclusive provider of a wide range of innovative products and services that are integral to a successful Games.
About GE - Advanced Materials
The Advanced Materials business of General Electric Company is part of the Industrial business group and is headquartered in Wilton, Conn. Comprised of Silicones and Quartz, GE - Advanced Materials is a global leader in providing a range of high-technology materials solutions. The GE - Advanced Materials, Silicones’ portfolio includes silicone-based products and technology platforms, silanes, sealants and adhesives. The Quartz portfolio includes high-purity fused quartz and ceramics Materials. These materials solutions are used as catalysts for innovation in hundreds of consumer and industrial applications ranging from car engines to biomedical devices to integrated circuits. Markets served include aerospace, agriculture, appliances, automotive, construction, electronics, furniture and furnishings, healthcare, home care, industrial, lighting, packaging, personal care, plastics, semiconductor, telecommunications, tire, transportation, and water purification. As a Worldwide Partner of the Olympic Games, GE is the exclusive provider of a wide range of innovative products and services that are integral to a successful Games. Experience more at www.ge.com/advancedmaterials.
® INSORB|20 is a registered trademark of Incisive Surgical, Inc.
* Lexan, Ultem, Cycoloy, Noryl, PPO, LNP, Colorcomp, Thermocomp, Lubricomp and Tufel are trademarks of General Electric Company.
® Bioject and Biojector are registered trademarks of Bioject.
® Airplus is a registered trademark of Implus Footcare, LLC.
™ Invisigel is a trademark of Implus Footcare, LLC.
* Addisil is a trademark of General Electric Bayer Silicones GmbH.
(1) Biocompatibility: A representative lot of material tested either by ISO 10993 or USP Class VI protocol. Test data available via Type I or Type II letter. Type I Letter: Issued for products that have been specifically tested for biocompatibility. Type II Letter: Issued when specific product has not been tested but similar products have been tested for biocompatibility.