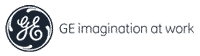
16 Nov 2005
Answers from the Experts: A Conversation with Clare Frissora of GE - Plastics on Materials for Medical Devices
Q. What are today’s most important considerations affecting medical device design?
A. There are three significant aspects to innovation in healthcare: enhancing speed, providing or enhancing safety, and managing total cost. When considering the optimization of medical device design, the goals are typically improving ease, speed, effectiveness, and safety of device use. To achieve these goals, designers are looking at multiple factors including miniaturization, weight reduction / custom weighting, and ergonomics.
For example, in the case of surgical instruments, minimally invasive surgical (MIS) instruments offer the opportunity to reduce patient trauma as well as improve safety and effectiveness by making these devices smaller, which means that smaller incisions are required to access the injured or diseased area.
Lighter weight is another key benefit for doctors and patients alike in certain devices such as wrist fixators. These devices are used to treat certain kinds of bone breakage such as Colles Fractures, a fracture at the wrist joint due to a fall on an outstretched hand, or other injury requiring wrist distraction. Traditionally, metal rods with screws were attached to bones to maintain stabilization while healing. But metal can make these devices heavy for the patient and can impede getting dressed. A plastic wrist fixator, made of Lexan* resin or Ultem* resin, however, enables the device to be slim and light, thus helping with mobility and comfort. Lexan resin not only reduces weight, but is also impact resistant, even after repeated exposure to gamma or with some newer Lexan grades, improved steam sterilization performance. Ultem resin offers greater exposure to autoclave sterilization at higher temperatures.
Q. So smaller and lighter devices can reduce the impact on patients – but what about the benefits to clinicians?
A. In the case of the wrist fixator devices, plastic materials also offer radio-lucent capability (invisible to x-rays), enabling doctors to more easily monitor the bone healing process. The benefits to both patient and doctor are exemplified in the Clear Wrist Fixator by Rigid Orthopedics where Lexan HPS7 resin, one of our new products was utilized to help achieve these application requirements of impact resistance, clarity, light weight, and gamma sterilization capability.
In devices being used directly by the doctor or nurse, ergonomic design can become very important. For example, a single-patient surgical instrument for surgery, though discarded after the procedure, may be used many times during the procedure; comfortable grip and functional design are important to facilitate proper use and functioning of these devices.
Another example where ergonomics and performance are also key is demonstrated with the INSORB®|20 subcuticular skin stapler from Incisive Surgical. This skin stapler is molded from GE’s Ultem resin, which helped provide an ergonomic design for a more comfortable grip interface with the hand. Ultem resin was also used because of its compressive mechanical strength and chemical resistance. The INSORB|20 stapler deploys up to 20 subcuticular staples, and needed high mechanical strength in its nose, arm, and yoke components due to the force of compression. GE’s Ultem resin was chosen to handle these forces and pressures without losing dimensional stability or strength. Because it’s a high-performance plastic, Ultem resin offers lightweight and ergonomic design for easy handling by the doctor and may aid the surgeon or nurse from tiring or cramping while holding or manipulating the device.
Another example of weight and performance can be demonstrated through a very different device, a sterilization tray. A sterilization tray holds used devices during autoclave sterilization and may offer nurses or other staff lighter weight alternatives to carry when made of plastics versus metal alternatives. Plastics can offer the benefits of impact strength and durability. All together, these materials as used in a variety of devices, add value to both patients and hospital staff.
Q. Can plastics offer capabilities other than lightweight and design freedom that allow it to be utilized where metals have traditionally been used?
A. The wide variety of high-performance plastics available today offers a selection of different property combinations needed to meet diverse device requirements. GE’s Ultem and Lexan resin portfolios in the applications described above are just two examples of materials that offer strength as well as sterilization capabilities requireed in the industry. One of the most promising areas for metal replacement is the evolution of plastic compounds. Compounds can deliver very high performance, including mechanical strength, lubricity, wear resistance, and dimensional stability that facilitate tight tolerances of application specifications. For example, GE’s LNP* Lubricomp* compounds are excellent candidates for applications where lubrication and wear resistance are required and the GE’s LNP Thermocomp* compounds are known for their inherent toughness. This can be of particular importance when considering the precision design and operation of the many internal components to minimally invasive surgical instruments. Access devices, hand instruments, and electro-surgical devices, provide examples of how these high performance LNP Lubricomp and LNP Thermocomp materials, when coupled with the critical design elements of the OEM, facilitate the ability to accomplish device design and performance goals. An LNP Lubricomp material when designed with Ultem resin as the base resin, for example, offers a combination of stiffness, wear resistance, and low coefficient of friction (COF). The carbon fiber lubrication additive allows Ultem resin to maintain a very high modulus. These are important considerations when seeking to enable faster surgical procedures while maintaining or improving safety for the surgeon and patient. Finally, it is important to mention that in these situations, we have the ability to offer OEMs biocompatible materials for these healthcare applications.
Q. You also mentioned cost management as a trend in medical devices. How can using plastics reduce costs?
A. In certain cases, working with metal can be very expensive. In the example of MIS instruments, there are many different internal gears, levers, and yokes. When made out of metal, these parts may be machined for precision designs followed by lubrication for good wear resistance and lower friction. The secondary operations of machining and lubrication add steps that can increase costs. Plastics may offer the benefit of easier machining versus metals. Alternatively, when those parts are replaced with injection molded plastic parts, it is possible to eliminate these secondary operations. While initial investment in tooling is required, with the reduction or elimination of secondary operations, there is an opportunity to reduce total system cost. Further, a process like injection molding allows easier throughput than piece-by-piece machining, speeding up cycle times.
GE’s LNP Lubricomp or LNP Thermocomp specialty compounds, for instance, offer internal lubrication properties and structural reinforcement to provide wear resistance and strength, plus precise tolerances required for gears and other internal parts. Both GE material product families may be suited for a variety of complex moving parts in endoscopic and other MIS devices such as trocars, retractors, staplers, and electrocautery devices.
Q. So plastics are being used to replace metal for internal as well as exterior parts?
A. Absolutely. Take an MIS device molded with our materials. These devices have a number of exterior parts such as triggers, buttons, and release levers that were converted years ago from metal to plastic using highly filled materials to maintain strength reinforcement but allow migration to injection molded components. Recently, more and more internal components are converting from metals to our resin technologies as we continue to innovate new solutions. There’s much compressive force on these parts so they require outstanding mechanical strength, need to be load-bearing, and need to work the same way every time for predictable interaction with the surgeon. Materials such as Ultem resin offer compressive strength and stiffness; LNP Thermocomp specialty compound offers a range of materials with internal reinforcements; and LNP Lubricomp compound offers reduced COF, improved lubricity, and wear resistance. In summary, plastics offer the ability to consider customized performance solutions yet eliminate secondary operations and enable injection molded processing.
Q. How do plastics compare to metals regarding sterilization?
A. Many devices require sterilization such as gamma or autoclave sterilization. That, in turn, calls for plastics that are capable of being exposed to irradiation or higher heat found in steam autoclave – for example 121-134 C. With autoclave sterilization, OEMs may call for the need to withstand repeated sterilization, from 2 to 2,500 cycles. The use of autoclaving has been accelerated by concerns for exposure to bovine spongiform encephalopathy (BSE, TSE/transmissible spongiform encephalopathy), commonly referred to as mad cow disease.
GE has developed innovative materials such as Lexan 4404 resin that can withstand these high heats, but offer lighter weight than metals. Lexan 4404 resin is a clear polycarbonate designed for use in devices exposed to limited multiple autoclave cycles, at temperatures up to 134 C. It’s a potential fit for a variety of surgical instruments and healthcare support equipment. We’ve also developed gamma-stabilized materials such as Lexan HPS7 resin, which offers lipid resistance with gamma radiation and multiple autoclave cycle capabilities in one product. Where there are requirements for higher number of autoclave cycles, Ultem resin and Noryl* resin may be considered. Ultem resin offers transparency and opaque Noryl resin offers even greater ductility. Both may be injection molded, thermoformed, and machined.
When color coding is needed by the OEM, LNP Colorcomp* specialty compounds can draw from a wide range of polymers and can bring custom colors for identification purposes to the device manufacturer. So we can find many examples of high performance plastics being utilized in situations that have been traditionally regarded as metal-only components.
Q. How is GE investing in developing new materials for the healthcare industry?
A. GE has a dedicated team of healthcare industry managers to build specialized expertise and knowledge so we can design and develop materials focused on the needs of healthcare device manufacturers, clinicians, and patients. We have invested in new laboratory testing and evaluation equipment that enables us to better assess the performance of our materials in medical applications. We also have increased our portfolio of products by about 20 percent in the last year, including new capabilities for autoclaving and new materials for smaller, more intricate parts as well as long or complicated flow lines. Lexan HPX8R, Lexan HPX4, and Lexan HP1HF resins mark new improvements to autoclavability, ductility, release, and flow. Finally, our ongoing innovations in our LNP specialty compounds allows us to respond to the many challenges of medical device design.
Reader enquiries
GE PlasticsPlasticslaan 1
4600 AC Bergen op Zoom
Netherlands
Helen Vandebovenkamp
helen.vandebovenkamp@ge.com
Tel: +31 164 29 20 97
Fax: +31 164 29 10 66
Netherlands
+31 164 29 20 97
helen.vandebovenkamp@ge.com
www.geplastics.com
Notes for editors
About GE - Plastics
GE - Plastics is a global supplier of plastic resins widely used in automotive, healthcare, consumer electronics, transportation, performance packaging, building & construction, telecommunications, and optical media applications. The company manufactures and compounds polycarbonate, ABS, SAN, ASA, PPE, PC/ABS, PBT and PEI resins, as well as the LNP line of high-performance specialty compounds. GE - Plastics, Specialty Film & Sheet manufactures high-performance Lexan sheet and film products used in thousands of demanding applications worldwide. In addition, GE - Plastics’ dedicated Automotive organization is an experienced, world-wide competitor, offering leading plastics solutions for five key automotive segments: body panels and glazing; under the hood applications; component; structures and interiors; and lighting. As a Worldwide Partner of the Olympic Games, GE is the exclusive provider of a wide range of innovative products and services that are integral to a successful Games.
* Lexan, Ultem, LNP, Lubricomp, Thermocomp, Noryl and Colorcomp are registered trademarks of General Electric Company.
® INSORB|20 is a registered trademark of Incisive Surgical, Inc.
Also available in