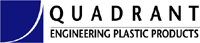
20 Oct 2004
QUADRANT ENGINEERING PLASTIC PRODUCTS EXTENDS BENEFITS OF REACTION INJECTION MOULDING TO NYLON MATERIALS
TIELT, BELGIUM – K 2004 – Low-pressure moulding methods, such as reaction injection moulding (RIM), have extended the economies and design benefits of injection moulding to applications once limited by mould cost, volume or processing challenges. Now, Quadrant Engineering Plastic Products (QEPP) is extending the benefits of Low Pressure Casting (LPC) to nylon-based materials.
Machining plastic components from standard shapes is effective for low-volume runs of small parts with simple Shapes. Injection moulding, however, has traditionally been more cost-effective for low part weights and medium to high series. Low Pressure Casting technology bridges the cap and offers a solution to the limitations in sizes and shapes of injection moulding and variations in wall thicknesses within one part.
Low Pressure Casting processes have altered that equation by improving economies of plastic parts that range from a few grams to several kilograms in weight, no wall thickness limitations and that run in series from a few hundred to a several thousands parts per year. LPC’s lower processing temperatures and injection pressures also enable the use of aluminium tools rather than hardened tool steel, further benefiting small volume series and parts produced for evaluation purposes. Generally tool cost can be up to half of injection moulding moulds.
Polyamide is among the few thermoplastic materials that may be processed either from pellets or by monomer casting, in which monomer is polymerized directly in an aluminium mould. Although QEPP, for years, has used monomer casting to produce its nylon stock rod, plate and tubular shapes, it has now adapted LPC processes to handle nylon-based monomers.
“LPC processing offers designers and end-users the economies of injection moulding combined with flexibilities in part size, geometry and tooling cost,” said Peter de Bruijn, Custom Castings Business Manager of QEPP.
“Now, these benefits may be further combined with the performance benefits of nylon materials, including high bearing and load capacity, excellent wear resistance, resiliency, vibration dampening and noise reduction.”
LPC processes combine two low viscosity liquid streams – mostly comprising monomer – with a carefully controlled amount of reaction catalyst and initiators. The subsequent chemical reaction forms polymers that grow in molecular weight until the reaction is finished and the monomers are transformed into a rigid, solid polymer.
Reader enquiries
Quadrant EPPHardstrasse 5
5600 Lenzburg
SWITZERLAND
Switzerland
+ 41 62 8858 150
contact@qplas.com
http://epp.quadrantplastics.com
Notes for editors
Quadrant Engineering Plastic Products (QEPP) is the world leader in the manufacture of engineering plastics in stock shapes (rod, plate, tube) for machining. QEPP also produces custom nylon castings and finished components. QEPP’s General and Advanced Engineering Plastics portfolio includes the broadest range of standard and custom shapes for machining and is available through its worldwide operations, technical support centres and authorized distributors.
The Quadrant Group is a global leader in high-performance polymer material solutions in the form of semi-finished and finished products. These specialty engineering thermoplastics and composites are superior in performance over metals and other materials, and are used in a growing number of applications developed with leaders in a wide range of industries.
Learn more about Quadrant at www.quadrantplastics.com.
ERTALON®, NYLATRON®, ERTACETAL®, ERTALYTE®, CESTIDUR®, TECHTRON®, KETRON®, FLUOROSINT® and SEMITRON® are registered trademarks of the Quadrant Group.
Related images

Quadrant Engineering Plastic Products (QEPP) is extending the benefits of Low Pressure Casting (LPC) to nylon-based materials.
Quadrant Engineering Plastic Products