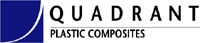
6 Jun 2007
COMPOSITE SANDWICH PANELS PROVE IDEAL FOR BUILDING FORMWORK SYSTEMS
Plastics panels made by Quadrant Plastic Composites for Hünnebeck work better, last longer than wooden ones
LENZBURG, SWITZERLAND – June, 2007 – Replacing plywood with high-performance composites may appear at first sight to be a prime case of over-engineering. But there is good reason to believe that a new formwork product from German company Hünnebeck, one of the world's top suppliers of formwork and scaffolding, will signal a paradigm shift in the industry.
Hünnebeck has just begun supplying concrete soffit formwork panels made by Quadrant Plastic Composites by sandwiching SymaLITE, a very light weight composite of polypropylene (PP) and glass fibres, between two skin layers of GMTex™ high performance glass reinforced thermoplastic (GMT). It introduced the new panels at Bauma, the international building and construction show in April.
Quadrant Plastic Composites is marketing the panels, which are covered by patents, within the Quadrant product family. They are direct drop-in replacements for plywood, fitting together inside the metal frames usually used. Tests at Hünnebeck indicate that they can be used up to 200 times, they come away easily from the concrete after it has set to leave a near-perfect surface, they can be nailed just like wood, they are easy to maintain, humidity does not cause them to either swell or rot, they are highly damage resistant but also easy to repair and recycle.
“There is a trend in the building industry to replace all-plywood panels with either plastic coated panels or all-composite ones,” says Quadrant Plastic Composites business line leader Non-Automotive Nicola Adamo. “This trend is linked to the need for better quality and longer-lasting panels, particularly for rented formworks and for formwork used for visible surfaces.”
“Furthermore, higher prices, lower availability and declining quality of traditional plywood are pushing in favour of a full composite solution.”
According to Adamo, plywood panels simply with plastic skins represent an improvement over traditional panels impregnated with phenolic resin, but they still have some disadvantages linked to the wooden core and to the different thermal expansion coefficients of the skin and the core. Humidity can still penetrate the core through nail holes or cuts in the plastic film, causing local swelling for example.
An alternative composite solution uses a PP foam core bonded to aluminium skins covered with PP foil. Quadrant Plastic Composites solutions however, are metal-free, which makes them lighter, but they still have better mechanical properties, thanks to the very high performance GMTex™ skin. They are also easier to nail and to recycle.
The colourable panels can be produced in thicknesses from 5 mm up to around 35 mm, in dimensions of up to 2400 by 4900 mm. The TOPEC system calls for panels 11 mm thick, in two main sizes, 1800 by 1800 mm and 900 by 1800 mm. Area weight is 7.7 kg/m2.
The panels supplied by Quadrant Plastic Composites are a little over 1 mm thicker than dry plywood panels, but they do not swell in use. Depending on their thickness, they are also about 8-15% heavier, but this difference is reduced nearly to zero once the traditional plywood has absorbed the humidity around.
Adamo says that the panels’ resistance to humidity and their very high impact resistance mean that they could also be adapted for use as scaffold panels and suspended floors for external use, as well as any other application where safety and water resistance coupled to long life are needed. Outside the building and construction industry, walls and floors in truck and trailers as well as shipping containers could be other potential applications.
The newly developed Quadrant Plastic Composites sandwich panels are the result of an internal development project at Quadrant Plastic Composites, initiated by its marketing department. “We handled the project exclusively until preliminary solutions were presented to the market,” says Adamo. “The final product is a joint development between us and Hünnebeck.”
Quadrant Plastic Composites has been supplying similar types of panels to customers working in building and construction in the Far East for several years, but they were not suitable for the European market. “Hünnebeck selected our panels because they meet its total systems requirement,” says Adamo.
“This is our first big non-automotive application in the construction industry,” says Adamo. “This is a real breakthrough for us.”
Reader enquiries
Quadrant Plastic CompositesHardstrasse 5
CH-5600 Lenzburg
Switzerland
+41 62 885 81 50
qpc@qplas.com
www.quadrantcomposites.com
Notes for editors
About Quadrant Plastic Composites
Quadrant Plastic Composites is the world’s leading manufacturer of glass mat thermoplastic (GMT) composites. The semi-finished sheet form is processed into sophisticated components, primarily for the automotive industry, using large-volume pressing processes; these components satisfy the highest safety standards, as well as featuring low weight compared to materials such as metal.
Learn more about Quadrant Plastic Composites at www.quadrantcomposites.com
About the Quadrant group
Quadrant, a global leader in high-performance polymer materials in the form of semi-finished and finished products with locations in 18 countries, generates annual sales of over CHF 800 million. The specialty engineering thermoplastics and composites manufactured and marketed by more than 2’400 employees worldwide are superior in performance to metals and other materials and are used in a growing number of applications, primarily in the capital goods industry. Together with leaders in a wide range of customer markets, Quadrant is continuously developing new areas of application. Thanks to its clear strategic orientation and focus, Quadrant has generated substantial added value for customers and shareholders since it was established in 1996 and is well prepared to continue expanding its market leadership in future.
Learn more about Quadrant at http://www.quadrantplastics.com